Accelerated Weathering with Xenon Arc: Ensuring Long-Term Automotive Material Performance
Jun 30, 2025
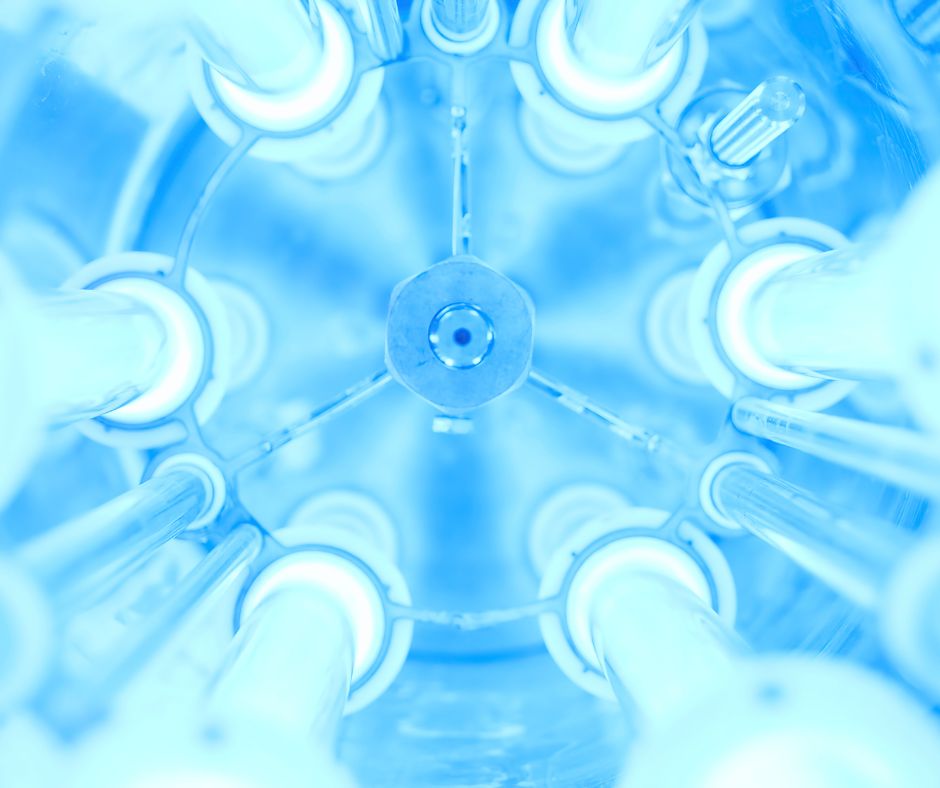
In order to balance aesthetics with long-term durability, xenon arc weathering is a primary solution to ensure materials withstand harsh effects of sunlight to vehicle design. In this instance, accelerated weathering testing uses a xenon arc chamber that can generate valuable data on the performance of materials.
By simulating real world environmental conditions, xenon arc testing can show how materials degrade over time due to solar UV radiation. This type of test will help to minimize the risk of premature product failure, deliver fast stability screening of new materials, and help to control quality for the materials used in automotive interior and exterior components. These include:
· Plastics
· Textiles
· Paint-coated parts
· Rubber
· Leather/vinyl
Xenon arc weathering testers are designed to mimic the damaging effects of short-wave UV and visible light from sunlight. Xenon arc lamps contain too much short-wave UV to allow beneficial correlation to natural exposures on the Earth’s surface. To reduce unwanted radiation and achieve an appropriate spectrum, various filters, such as daylight, extended UV, and window glass filters, are used to run the tests on a proper spectrum.
These filters, originally made of just glass, have come a long way over time due to extended trials and research. Typically, exterior and interior simulations will utilize different filters since the car windshield, windows, and body provide an additional layer of UV protection.
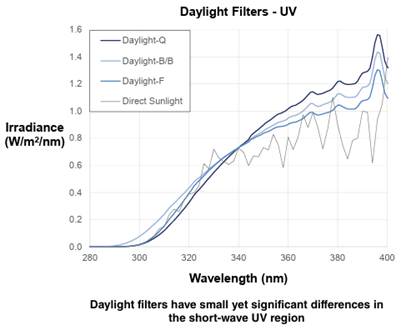
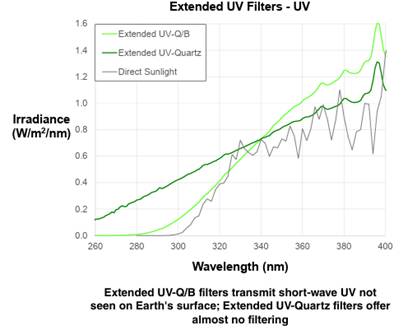
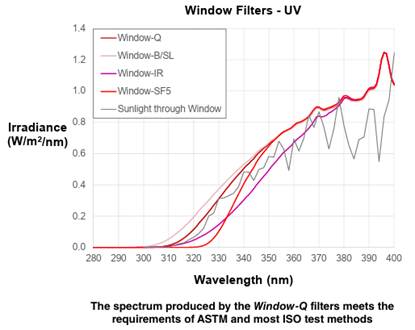
In a few days or weeks, the xenon arc tester can replicate the damage that happens over months or even years outdoors. Xenon Arc Weathering testing helps determine how long a material will keep its color and resist various conditions under extended sunlight. These conditions include:
- Cracking
- Fading
- Peeling
- Color change
- Embrittlement
- Tackiness
- Chalking
- Gloss change
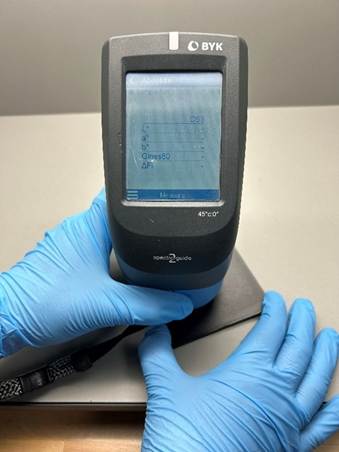
Xenon Arc Capabilities
MGA offers extensive capabilities to perform xenon arc weathering testing. With the use of Q-Lab’s Q-SUN Xe-2 and Xe-3 Xenon Arc testers, up to 55 samples can be tested simultaneously. Environmental conditions, including sunlight intensity, temperature control, and rain (with both front and back spray system), can be simulated with a 20 to 95% humidity range, a 25°C to 65°C chamber air temperature range, and a 25°C to 120°C black-panel temperature range. Evaluations of aesthetic change can be measured, including:
- Gloss change using glossmeter as per ASTM D523 & ISO 2813.
- AATCC Grey Scale readings as per ISO 105/A02.
- Color changes through spectrophotometer like handheld BYK spectro2guide as per SAE J1545, ASTM E1164 with 2-degree or 10-degree observer, CIE standard illuminant D65, 45°/0° measuring geometry.
- In certain instances, mechanical properties such as tensile strength, peel test, and adhesiveness are tested after exposure.
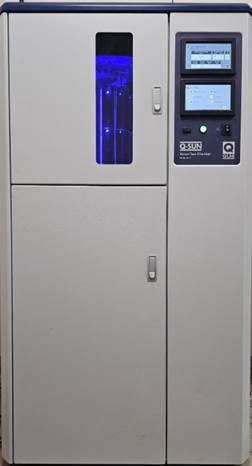
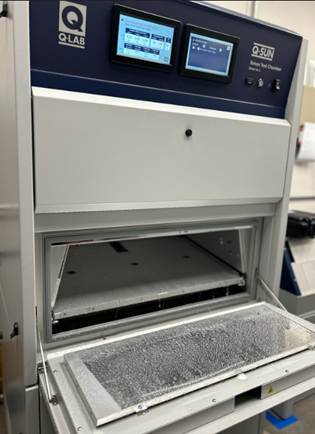
The samples are tested either as a coupon or part, depending on the requirements. Various interior and exterior components made of plastic, textiles, rubber, and paint coated parts, including front/rear bumpers, covers, brackets, seats, and door trims exposed to sunlight, can be simulated with a Xenon Arc tester to assess potential degradation over time.
Selecting the right material is essential to reduce damage from prolonged sunlight. In addition to the material type, factors such as additives and stabilizers, colorants and dyes, surface finish and texture, material thickness, moisture sensitivity, layered or composite materials, and processing conditions all play a key role in achieving an optimal balance of aesthetics and mechanical properties.
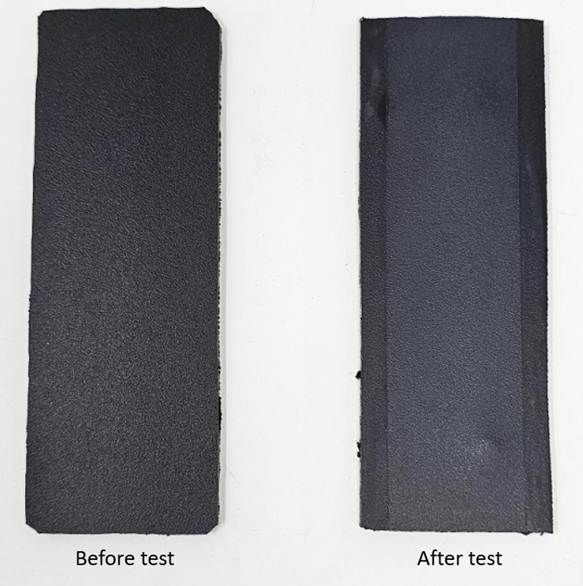
Our experienced engineers possess the knowledge and skills required to operate and execute tests successfully. Our engineers finalize tests by assessing and reporting the results in accordance with our quality-controlled procedure.
Common Test Standards
· AATCC 16.3 – Colorfastness to Light
· ASTM G155 – Xenon arc exposure for Non-Metallic materials
· SAE J2527 – Accelerated testing on automotive exterior materials
· SAE J2412 - Accelerated testing on automotive interior materials
· ISO 4892-2 – Plastics – Methods of exposure to laboratory light source
· ISO 11341 – Paints and varnishes – Artificial weathering and exposure
· Ford BO 116-01 – Resistance to Interior weathering
· GMW 14162 – Colorfastness to Artificial Weathering
· GMW 14650 – Performance requirement for exterior plastic parts
· VW PV 1303 – Non-metallic Materials: Exposure test of passenger compartment components
· VW PV 1306 – Lightfastness for determination of tackiness of Polypropylene Plastics
· Tesla TP-0000701 – Lightfastness of materials to Artificial Weathering
· Toyota TSM0501G – Standard test methods for plastic molding materials
· Toyota TSM0601G – Criteria for test for quality of color change by aging
· Toyota TSH3130G – Paint film quality for interior painted parts
The MGA Advantage
By utilizing xenon arc testing, MGA’s capability provides a fast and reliable way to evaluate long-term performance of automotive materials under simulated environmental conditions. With our Q-Lab equipment and knowledge of industry standards, MGA provides expert support to help customers reach their goals of material quality and occupant safety.
This capability is available at our facilities in California, Texas, South Carolina, Alabama, Canada and soon-to-be Mexico. For more information, please reach out to us via our contact form on our website.
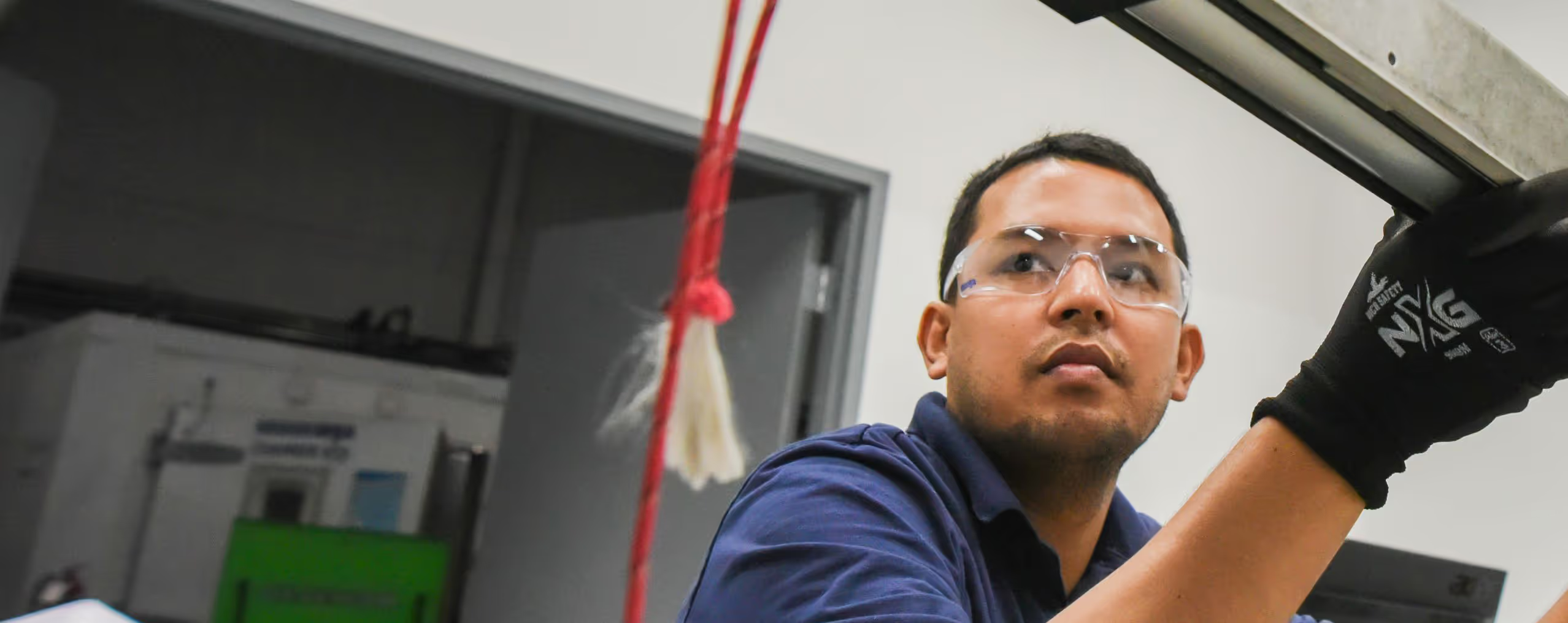
Ready to Get Started?
Let's discuss your testing needs and how MGA can help. Our team is ready to provide the expertise and solutions you're looking for.