Mechanical Shock Testing: Improving Battery Performance
Jul 10, 2025
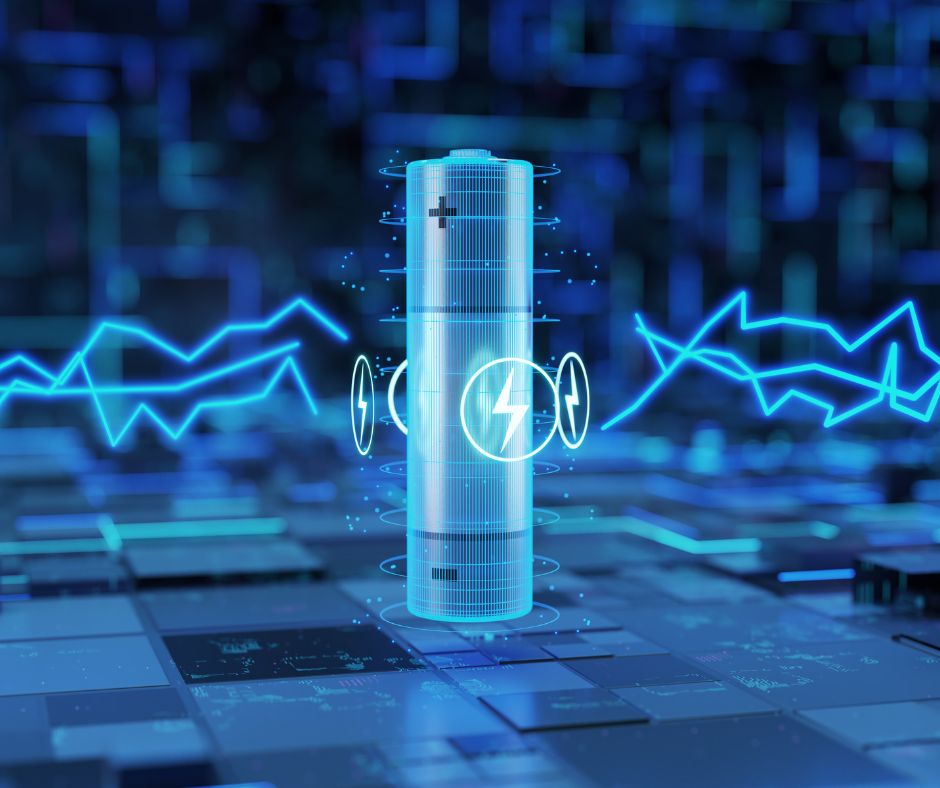
In today’s world, advancements in technology and a push for reliance on clean and renewable energy sources are increasing rapidly. Batteries can be found powering nearly everything, from the smartphones in our pockets, the electric vehicles we drive, and even the satellites up in space.
As their use becomes more widespread, ensuring the safety and reliability of these batteries and their components through specialized testing is crucial. One essential aspect of the testing process is mechanical shock testing.
MGA has an extensive history supporting battery testing, including mechanical shock test modes. As we continue to move the industry forward by offering multiple solutions to accommodate a wide range of test articles and shock requirements.
Importance of Mechanical Shock Testing
Often mistaken for vibration or electrical shock testing, mechanical shock simulates a unique environment that a test article may encounter.
Mechanical shock testing helps evaluate how a component responds to sudden, forceful impacts that mimic real-world scenarios such as drops, impacts, collisions, or abrupt movements. For example, in automotive applications, these tests could simulate the impact of potholes, or handling drops during assembly, and shipment. These tests are essential for identifying potential failures that could lead to decreased performance or loss of function.
In more severe cases, hazardous situations, like leaks or fires, could occur. Whether in electric vehicles, power tools, or consumer electronics, ensuring that batteries can withstand these shocks is important for both safety and long-term reliability. By understanding how mechanical stress affects battery integrity, manufacturers can refine designs to enhance durability and overall performance.
Mechanical Shock Test with MGA Pyroshock System
Incorporating mechanical shock testing into the battery development process offers several benefits:
- Safety: Identifies vulnerabilities that could lead to battery rupture, leakage, fire, or explosion, particularly in lithium-based batteries.
- Mechanical Integrity: Ensures batteries can withstand physical stresses encountered in applications like automotive, consumer, and military devices throughout their expected life cycle.
- Performance: Verifies that a battery’s performance does not degrade after being subjected to everyday use and potential misuse.
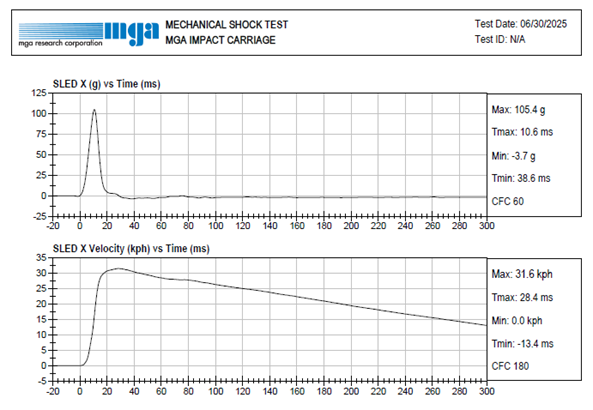
Mechanical Shock Testing Methods
MGA utilizes various test equipment to thoroughly evaluate batteries during and after a mechanical shock. Each of these methods exposes batteries to sharp, high-G acceleration pulses in different orientations to simulate real-world mechanical shocks. Depending on the size and specific nature of the test article, from a single cell all the way up to a full pack, the most suitable piece of equipment is chosen.
- Shaker Table: While also being able to perform a standard mechanical shock test, shaker tables offer the unique capability of longer-duration vibration testing. These tests are often performed in tandem to understand how continuous, repetitive stresses, combined with sudden impacts, affect battery performance and longevity.
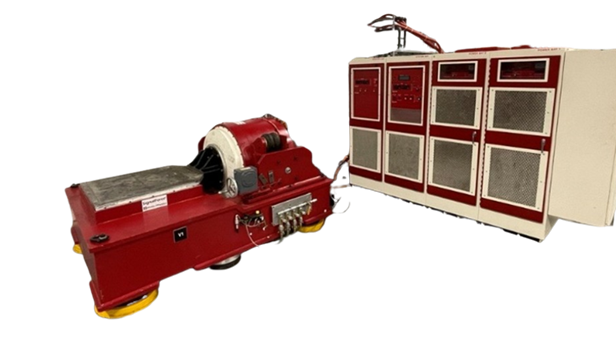
- Drop Tower Shock Test Machine: This form of testing utilizes a pneumatically operated platform that is dropped onto an elastomer pad to perform the mechanical shock. These pads are preselected and can be interchanged to achieve the desired pulse shape, including half-sine, square wave and sawtooth, as well as the pulse duration. A key advantage of this machine is the high degree of consistency. After programming the system, this testing can be automated to deliver rapid and highly repeatable shocks, allowing for lifecycle shock testing simulations of the test article.
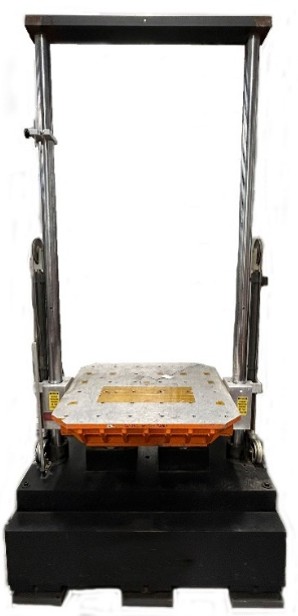
- Acceleration Sled: Sled testing is similar in many ways to an actual crash test as it creates a simulated acceleration shock, known as a ‘crash pulse’ within the automotive industry, to replicate the forces seen in a crash test. MGA’s Acceleration Sled System uses a sled carriage that is positioned against a pneumatically powered thrust column and accelerated along a fixed set of rails. This method is ideal for mechanical shock tests on larger test articles, specifically full electric vehicle battery packs. The advantage of sled testing is that the test article can be subjected to the exact shocks seen in an actual crash test, without the need for a full vehicle, allowing for the battery to be evaluated in a safe and highly repeatable environment.
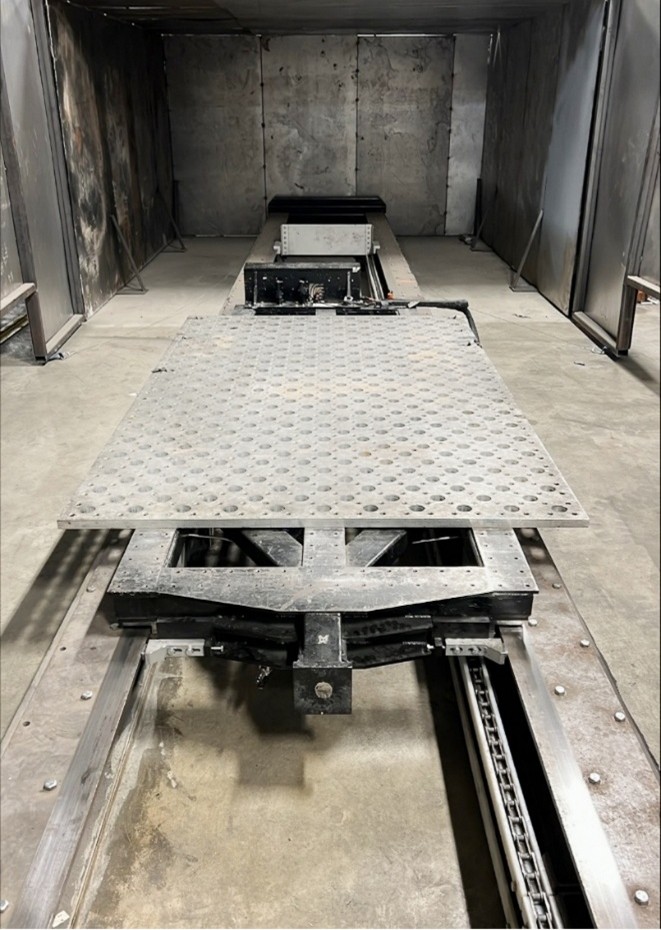
- Impact Sled: Although this approach is similar to MGA’s acceleration sled testing, the main difference is how the shock is actually generated. Rather than using the thrust column itself, the ‘launch’ carriage is positioned against the thrust column and accelerated into a stationary ‘target’ carriage positioned further down the track, upon which the test article is located. Impact attenuating material is placed at the contact point between the two carriages to achieve the desired acceleration characteristics. Like with the drop tower shock test machine, the shock profile is typically a half-sine shape, with short duration and high acceleration magnitude parameters, but without the size limitations commonly encountered. This is ideal for situations where the test article, particularly complete battery packs, need to be subjected to these types of shocks, but may not fit with other equipment options.
Carriage to carriage impact sled at MGA Wisconsin
- Pyroshock: This form of mechanical shock testing is unique as it is specifically designed to simulate pyrotechnic or other severe events a spacecraft might experience during flight such as ignition, launch, separation, and re-entry maneuvers. MGA’s Pyroshock System has been designed in-house and proven within the industry to replicate these shocks on critical components, like batteries, for the space and defense industry. When a mechanical shock test requires extreme accelerations, in some cases greater than 20,000 G’s, the pyroshock equipment is the perfect solution.
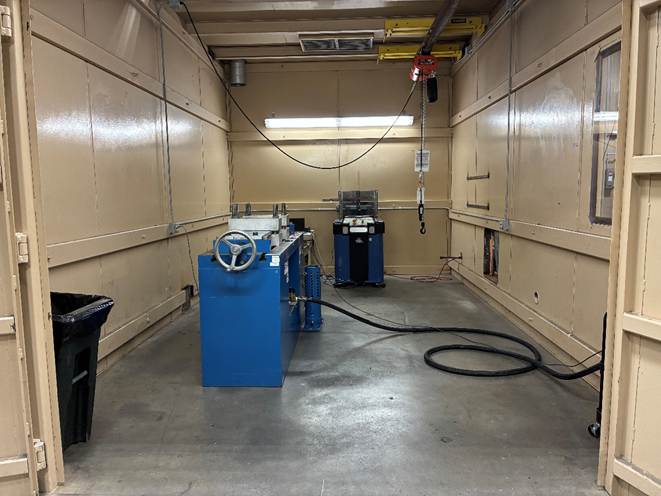
Supported Testing Standards for Mechanical Shock
MGA's testing services align with several key standards, including:
- UN/DOT 38.3 (UN Transport of Dangerous Goods): Outlines requirements for the safe transportation of lithium metal and lithium-ion batteries, encompassing tests for altitude simulation, thermal conditions, vibration, and mechanical shock.
- ECE R100 (Economic Commission for Europe Regulation No. 100): Specifies safety requirements and testing protocols for rechargeable energy storage systems (REESS) in electric vehicles, including mechanical shock tests to ensure battery integrity under impact conditions.
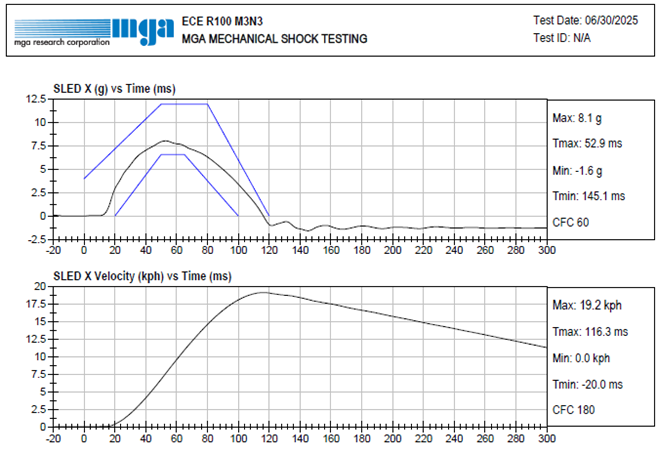
- ECE R136 (Economic Commission for Europe Regulation No. 136): Ensures that the batteries used in electric motorcycles meet stringent safety standards, providing a high level of protection to users and minimizing risks associated with battery use in these vehicles such as mechanical integrity, thermal management, electrical safety, environmental exposure, and fire resistance.
- SAE J2464 (Society of Automotive Engineers): Defines abuse testing for electric and hybrid vehicle rechargeable energy storage systems (RESS), including mechanical shock, drop, penetration, roll-over, water immersion, and crush tests.
- MIL-STD-810 (Military Standard): Provides a series of environmental tests to assess the durability of equipment, including batteries, under various conditions such as mechanical shock, vibration, and temperature extremes.
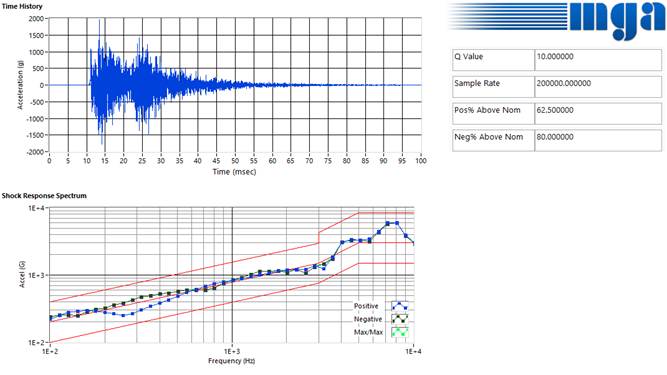
- DO-311: Published by RTCA (Radio Technical Commission for Aeronautics), specifies the minimum operational performance standards for rechargeable lithium batteries and battery systems used in aviation, including testing requirements for thermal runaway containment, mechanical shock, vibration, electrical safety, environmental, fire, and overheating.
MGA Facilities
MGA has experience performing electric vehicle battery tests at all levels: cell, module, and complete high-voltage packs. Our expert teams have the right training and proper equipment to safely execute all types of battery testing at our facilities in Michigan, New York, and Wisconsin.
When working with live battery components, MGA’s staff are trained to monitor pack isolation and work with our clients to identify and diagnose potential faults when communicating with the device through CAN systems. Testing is often performed within an MGA Containment Chamber in case a situation arises where the test article is no longer safe to interact with, or a thermal event is experienced.
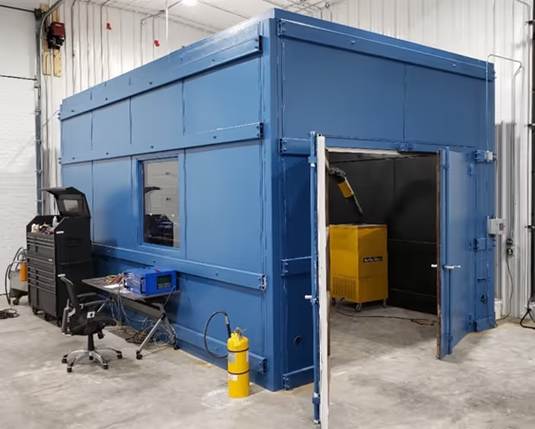
MGA Advantage
Mechanical shock testing is a vital component in the development of batteries, ensuring they meet stringent safety and performance standards. MGA Research Corporation's advanced testing facilities are equipped to provide comprehensive evaluations, helping manufacturers to deliver reliable and safe battery products to the market.
If you are interested in learning more about our testing capabilities, fill out our contact form today!
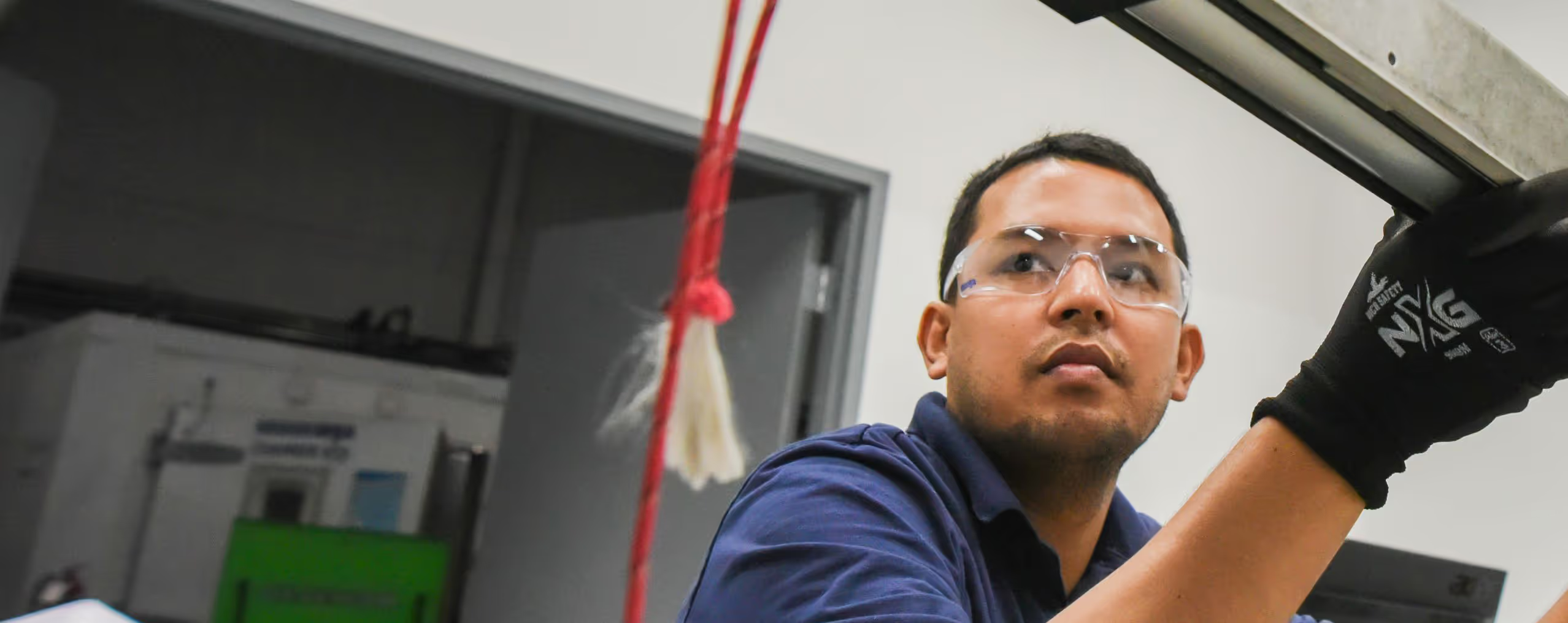
Ready to Get Started?
Let's discuss your testing needs and how MGA can help. Our team is ready to provide the expertise and solutions you're looking for.